Backordering is no longer a strange concept for many modern ecommerce businesses today. However, not all stores can accept backorders effectively and fulfill them accurately. Modern eCommerce merchants need to pay attention to backordering cost, challenges, and approaches to deal with them effectively. This article will cover the common challenges of backorders, as well as how to address them
Common backordering challenges and solutions
Challenge: Bottlenecks slow fulfillment
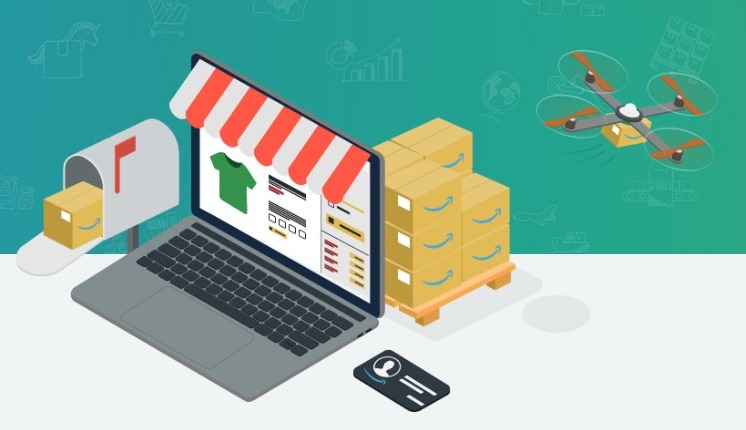
Slow fulfillment always makes the sellers and buyers wait for a long time to conduct selling activities as normal. It also interrupts business activities. There are several reasons, including natural disasters, unforeseen issues, material shortages, and so on.
Solution: Slow fulfillment is inevitable, but we still have some measures to minimize it. The business should develop its distribution network, and connect with different vendors and distributors to ensure they always have stocks to sell. Moreover, eCommerce businesses can use some tools to automate the fulfillment process, then it can run faster and reduce selling disruption.
Challenge: Lack of space
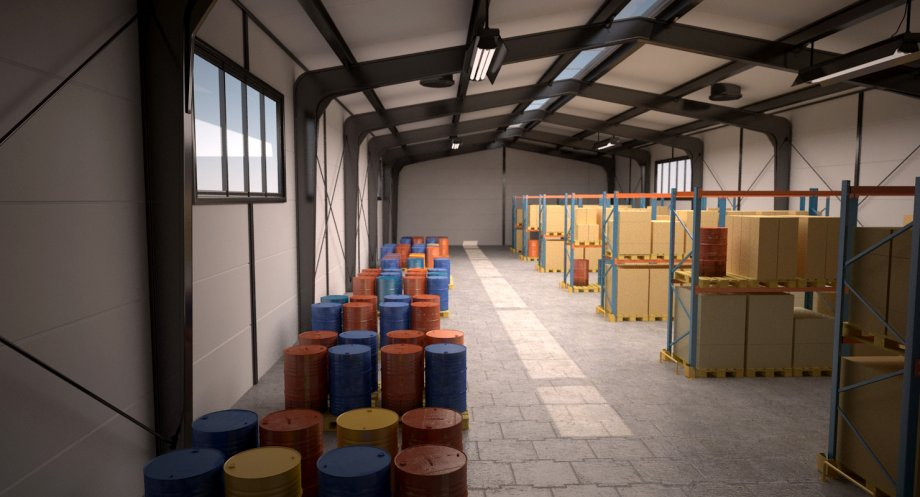
Another common backordering challenge is the lack of storage. The capacity of the warehouse is the main factor in deciding the levels of stocks your store can hold. Your business is expanding, and you may face a good shortage if your warehouse space is still small. Low inventory space limits the number of products supplied and thus reduces chances for customers to buy the expected items and make the fulfillment time of backorder longer.
Solution: One of the most popular approaches for small storage space is dropshipping. However, the business may gain a lower profit margin with dropshipping. If you still want to maintain a high level of profits during peak seasons, it would be better to use backorders. Therefore, the customers still can buy the items which are not in the warehouse and receive the shipment at a later date.
Challenge: Uncertain supply chains
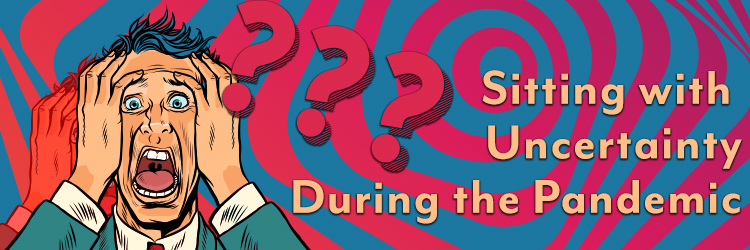
The pandemic as well as interrupted shipments and drastic shifts in supply and demand have slowed the global supply chain process. Natural disasters and slower-than-usual global shipping times can affect how quickly you get items to fulfill your backorders.
Solution: It’s hard to foresee all the uncertainties, but we can prepare plan B to deal with them. Backorder is the most powerful approach to confront sudden problems without stopping selling.
Challenge: Peak season demand

A drastic uptick in demand can cause backorder challenges, especially if you aren’t well prepared for them. The pandemic has changed much about consumer behavior, and even well-prepared stores may be having a hard time predicting peak season demand accurately
Solution: Utilize BigCommerce backorder as a useful measure to rescue your store from that situation. All you need to do is pre-set all the items as a backorder. When they go out of stock, the customers still can buy those products and receive the shipments at a later date. However, in the hot season, the quantities of back-ordered items will go up sharply, so you need to conduct an effective back ordering process to avoid delays. Moreover, to have better control over peak season demand, the data from selling records can help you analyze and forecast upcoming needs, and then you can prepare for the stocks as well as set for backorders.
Challenge: Running out of safety stock
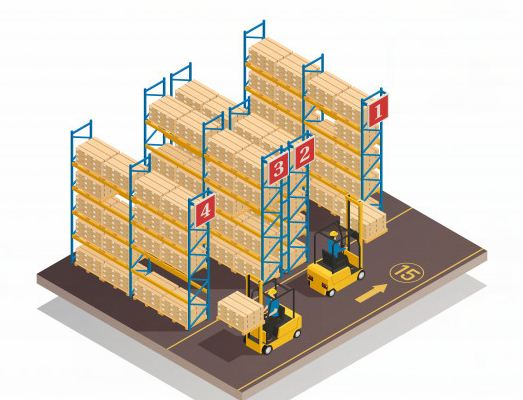
To plan for uncertainties and ensure effective backorder management, your store may have a certain safety stock level to avoid the out-of-stock situation. Safety stock level is a number of extra stocks used to maintain seamless selling and fill backorders. The higher safety stock level, the fewer rates of stockouts.
Solution: At first, you need to keep a reasonable level of safety stock level. As we mentioned, the demand will suddenly climb in those cases, but if your safety stocks are not enough or get aging, out-of-stock status still occurs, and you may need a lot of support for backorders.
3 Backorder management solutions for every eCommerce business
Atom8
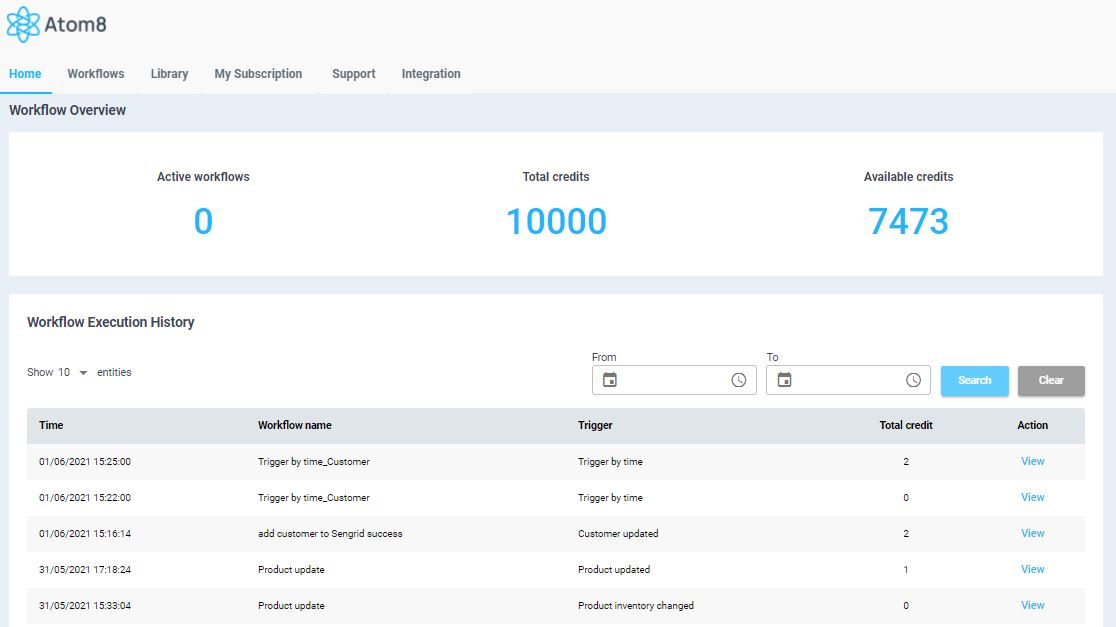
Keeping track of inventory status and fulfillment process, simple sheets, or hand-writing documents is insufficient. We may encounter mistakes that can affect the whole selling activity with traditional approaches. Atom8 is an automation app that can automate your business tasks following available or customized workflows. Therefore, you may feel it easier when using Atom8 to streamline the process and then visualize and display data on a spreadsheet. Then, you can realize which kinds of products can be out of stock in peak seasons and set them as backorder in the BackOrder app.
BackOrdered
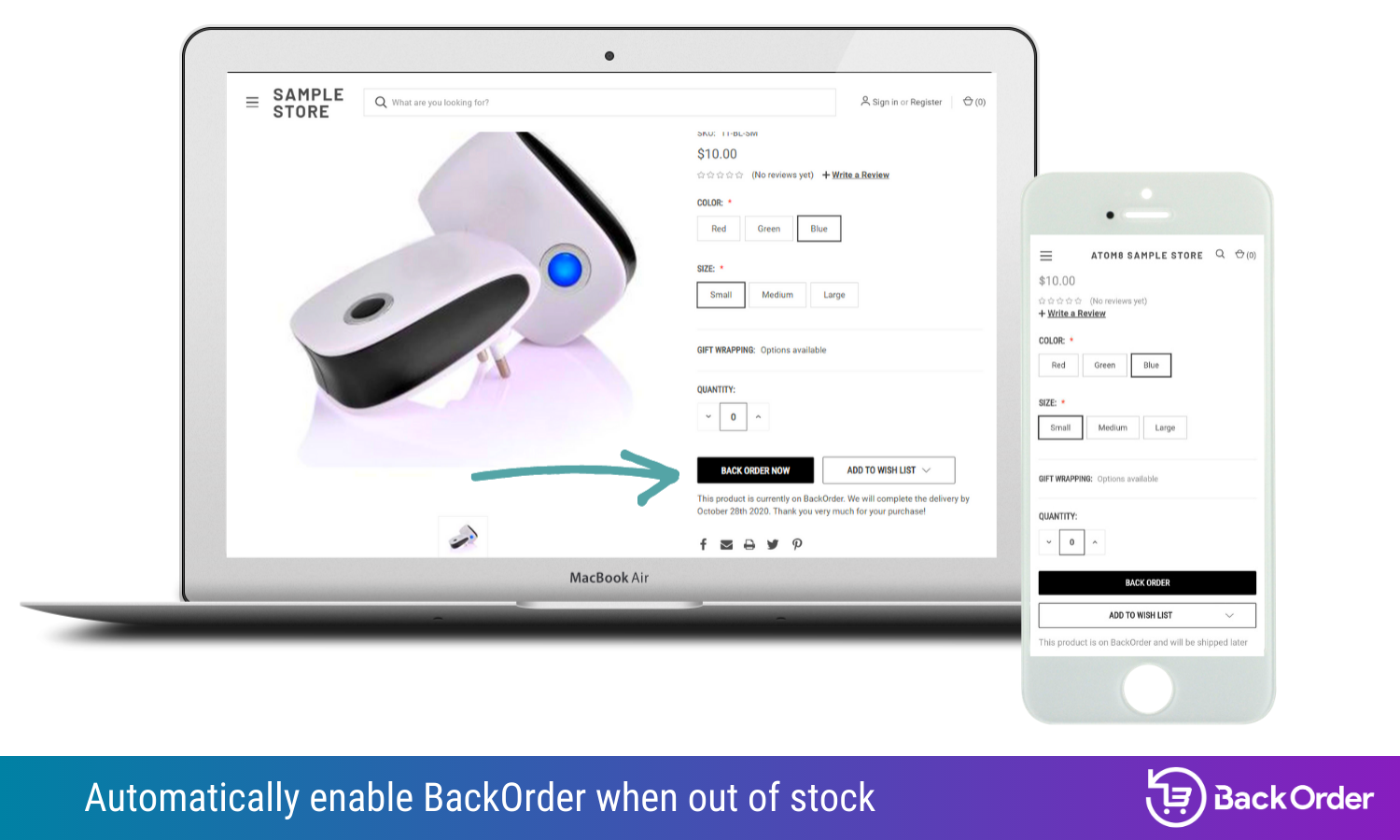
If your store is on BigCommerce, you can try the BackOrder app, which is an effective solution for your backordering cost and challenges. All steps you can do to get started with BackOorder is to pre-set all items considered high-demanded. Then when they run out of stock, the customers can still buy them as backorders.
Flxpoint
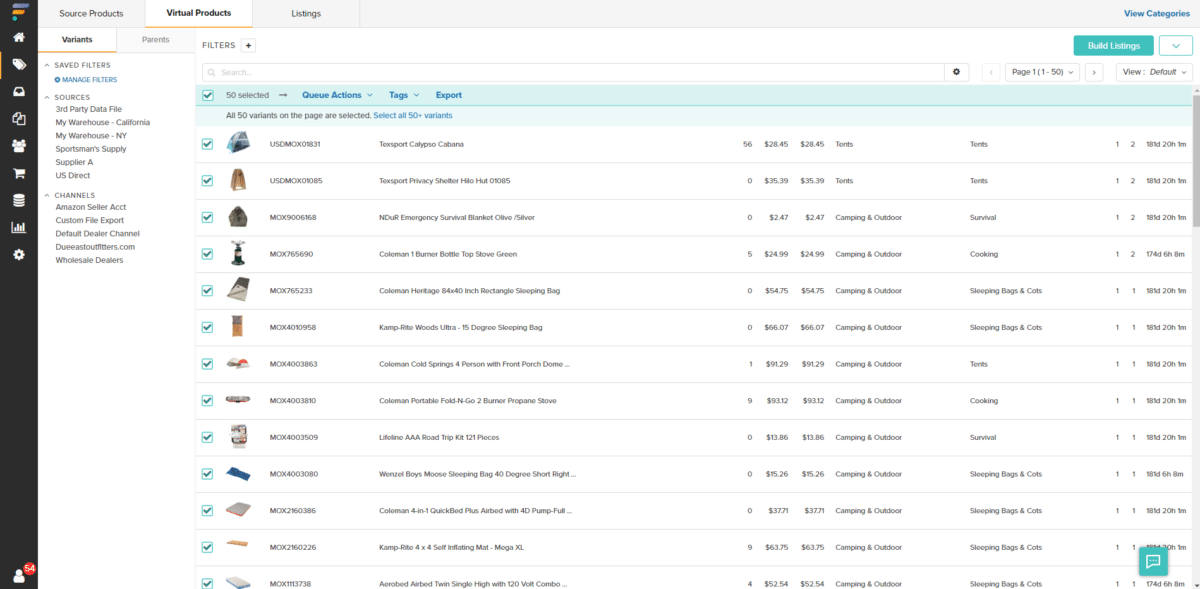
Flxpoint is an automation app that can unify and automate your business operation in different departments. In terms of inventory, Flxpoint can visualize the product catalog to help you feel easier to merge, prioritize and add product information. You not only have accurate product listings but also have a transparent and reliable view of inventory availability to come up with effective approaches to deal with stock problems. Moreover, this app helps to automate the fulfillment process so the business can save backordering cost.
Conclusion
Undeniably, we have to deal with many issues related to backordering cost and challenges. We also mentioned some alternatives, and we hope you can find your approaches from our suggestions.