Backorder Management Strategies for Peak Seasons
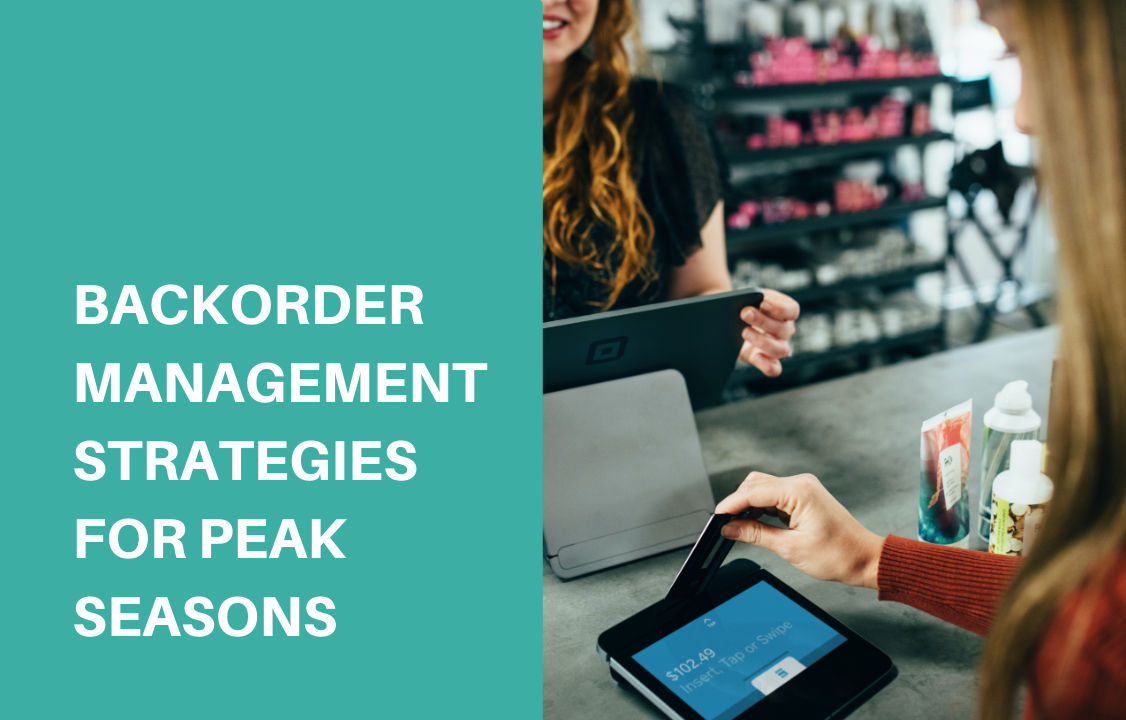
Not only in the festive period do we experience peak seasons in online business. Many retailers see a high volume of sales before Christmas or summer, whereas sports vendors get higher demands during sports seasons. This has urged businesses to leverage their backorder management strategies to keep up with expectations. No matter what time the peak season is, the importance is whether you are ready for it. The eCommerce industry is fully competitive, and you need to understand the best backorder management strategies to employ during high seasons. Here are a few tactics that might effectively assist you during peak seasons. Staff training Your staff poses a significant issue for your value chain every day, let alone during the peak seasons. Therefore, you need to prepare your staff for every unexpected situation with sufficient training and cross-trainings. Furthermore, have a distinctive plan for temporary staff so that you don’t waste so much time while still making the best out of your people. Nevertheless, you need to invest quality time to train your staff if you don’t want a negative review on your performance Most eCommerce businesses cross-train full-time associates through all departments, especially those involved with using equipment like forklifts. Review and Revise Sometimes, it is hard to address every order during peak seasons as you will be rushing all over the place. Nevertheless, once the volume decrease, you can review and revise the performance across departments. The goal is to identify your weaknesses to improve in the future. One of the worst situations is being out of stock, especially for hot-selling items. This not only drives your customers away but also devastates your credibility. To avoid this, review your backorder management strategies with your team to point out challenges and how to address them. This will enable you to improve sales later. Evaluate outsourcing Think about your business equipment and facilities, whether there’s sufficient room for more product during the high season. At times, you might need additional storage. One solution is to sell large inbound shipments, increasing warehouse spacing levels. Another option to consider is dropshipping or leasing additional storage for your products. After all, you have to ascertain if you have the necessary equipment to accommodate increased inventory stock. Keep customers updated about order status The delivery time is one of the most important factors affecting customer satisfaction. Therefore, don’t forget to keep an eye on the delivery status during peak seasons. Try to provide as many delivery options as possible, making it more convenient for your customer to purchase in your store. If you’re using multiple distribution centers, analyze the route so that the order would arrive at the fastest pace and the minimized costs. Use automation Managing backorder has never been easy, especially while having tons of orders that need to be fulfilled constantly. Hence a lot of businesses have relied on automation to work on the inventory. Through workflow with predetermined rules, the system will tell you when an item is low on supply. Then you might consider reordering if the demands are still high. This way, you don’t have to keep an eye on the inventory every time. What’s more, you can integrate this backorder system into your currently used workflow automation platform. This combination allows for centralizing your management, saving you the time and efforts to invest in more impactful activities. Conclusion Being out of stock is an absolute nightmare. Strategizing for a peak season for any eCommerce business is essential if you want to retain and improve your revenue. The key is to find out the backorder management strategies that work best for your store.
Backorder Management Step By Step
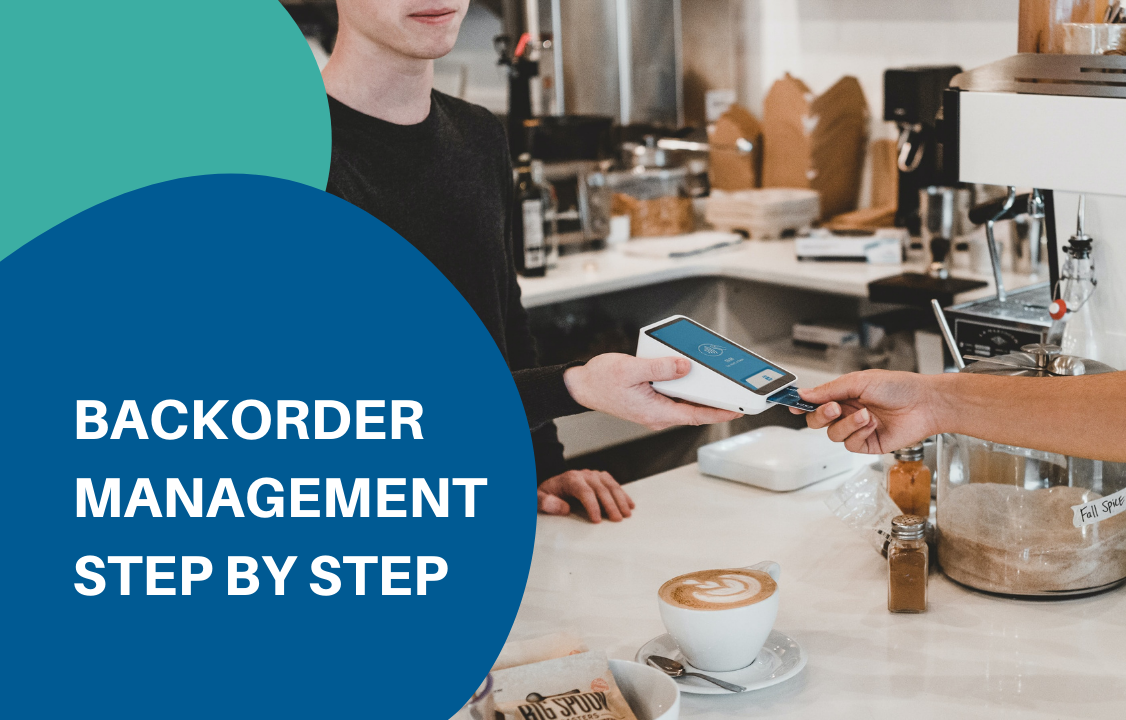
Backorder management takes care of goods that the company cannot fulfill because the demand is beyond the supply. Today, we use different complex terms to describe how companies keep goods flowing to their customers—for instance, LIFT, FIFO, MRP, ERP, and supply chain and demand. Yet there is one important term most people overlook and misunderstand, which is backorders. Unlike preorder, which is to order a product that has never been on the market, backorder referred to a currently running out item that can be fulfilled later. Backorder involves a process where goods are about to be reproduced, meaning that they can always be delivered in the future. Causes of Backorders Backorders from Gritglobal can do you well given a thorough understanding of the concept. In the later part of this article, you will learn the simple process to address your backorder issues. Before we start, let’s go through different reasons for backorders to happen. Unusual Demand An unusual demand might occur during the holiday or festive time. It might also be due to natural events such as hurricanes and disasters where a large number of goods are required in a short period of time. A lot of factors can contribute to a product getting an unusual demand from the public. Supplier issues We live in a supply chain that is stretched throughout the world, and at times there will be supplier issues. While it might not be intentional, nature can have its cause. Additionally, regulatory compliance, strikes, or shipping can cause suppliers to delay products. The disparity in order patterns Natural disasters, weather events, and holiday seasons can cause variations in order patterns. Companies might depend on demand planning models to foresee the total orders and customers. However, a sudden change in people’s demands can disrupt or throw manufacturers off-balance. Steps of Backorder Management process To avoid disappointing your customers because of your inability to fulfill their expectations, you need to follow a good backorder management process. Here are the steps of the backorder management process to implement for your business. Be transparent about product availability and shipment date In dealing with backorders, you need to indicate product availability and shipment date. With this, customers can decide if they want to wait for the product or not. Furthermore, it helps build trust with your customers that you value their time. Fulfill available items if possible Peradventure you have a limited amount of the product, you can perform partial fulfillment. For instance, you have three mobile phones in stock while there are two customers, each of whom wants two phones. Here, you can decide to fulfill half of the order while backordering the other. In other words, customers will receive a partial shipment of the product with an estimated time for the remaining to arrive. Place order for unavailable items In case of dropshipping, you can order the unavailable product from your supplier or manufacturer. It is essential to keep the customers informed about the current state of the product. Update customer on order status After a customer has placed an order for an item, they have the right to be informed about the current delivery status promptly. In the event that the product is no longer available for manufacturing, it’s crucial to notify them and initiate a refund. Effective backorder management ensures timely updates and appropriate actions in such scenarios. Receive restocked items and fulfill Once you receive the items, you can restock and fulfill the backorders. Remember to stick to the estimated time you indicated in your first message. If You’re on BigCommerce See How BackOrder Solves Your Pain Points Eliminate Lost Sales Due to Stockouts Many businesses struggle with losing sales when items are out of stock. BackOrder ensures you never miss a sale by automatically enabling backorders when inventory reaches zero, keeping your revenue steady. Streamline Inventory Management Managing backorders manually can be time-consuming and error-prone. BigCommerce BackOrder automates this process, integrating seamlessly with your IMS/ERP to schedule workflow smooth and accurate. Enhance Customer Satisfaction Uninformed customers can lead to frustration and lost business. BackOrder allows you to customize notifications and BigCommerce automate emails, ensuring your customers are always informed about stock status and expected restock dates. This transparency improves the customer experience and builds trust. By addressing these pain points, BackOrder helps businesses maintain consistent sales, streamline operations, and keep customers satisfied. If you have further question, please contact us!
Inventory Control Tips For Backorder Management
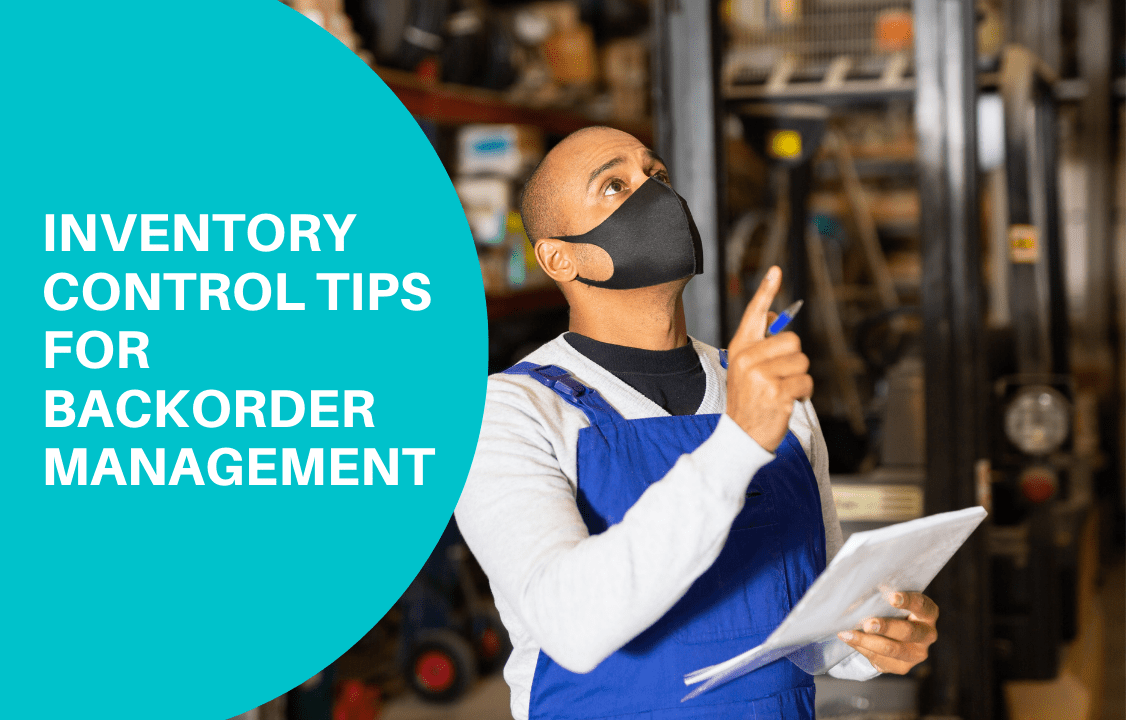
To have effective inventory control, you need to create a balance between minimizing the cost of holding a lot of inventory stock while maintaining adequate stocks for your customers’ demand. In most cases, out-of-stock orders can lead to customer dissatisfaction and lost sales. However, imagine having a customer order that can be filled later? What if the customer is willing to wait for the order? What is inventory backorder? A backorder occurs when a customer places an order or buys a product for inventory stock that is unavailable. An inventory backorder may arise when a product is sold out because of unforeseen high demand. Assuming you have a product with seven items in stock, three different customers decide to order the same product, with each desiring to buy four each. In a normal situation, you cannot fulfill one’s order and tell others to go. However, backorder makes it easier for you to sell two items to each and assuring them to receive the remaining items on a future date. Tips for inventory control When your online store is experiencing a surge in demand, there is every possibility you might have backorders. However, stock management is an essential aspect of increasing your conversion rate. Here are important tips for backorder management if you run an online business. Open communication with suppliers and customers Encourage open communication with your customers and suppliers. You can do this through email, chat, phone, or social media. When faced with a backorder, you can provide honest answers to ease the pressure. Ensure you display your contact information correctly on your website and reinforce the importance of customer satisfaction. Data-driven inventory control You need a data-driven inventory control such that orders won’t be placed if the distributor or wholesaler cannot fulfill the demand. When you have frequent backorders for several products in different locations, it involves a lot of data. Additionally, there must be accurate delivery within the stipulated timeframe. However, without a proper data-driven inventory management tool, backordering can become a significant issue. Once you face this situation, it will cause problems such as loss of business, customer trust, and brand credibility. Accurate warehouse inventory To avoid any backorder mishap, you need to keep an accurate inventory of your items in the warehouse. It can be hard to know the number of items available manually, but automation has made everything easier. Therefore, to avoid having backorder or out-of-stock orders frequently, ensure to keep accurate warehouse inventory. Review inventory frequently Here, you need to review your inventory frequently to ascertain what you have. It is important to look at your processing for ordering and stocking inventory if you experience backorder regularly. If you have historical data, it will help you when to reorder stocks before they get low. Furthermore, it can also use the auto-schedule reorders. Assign automated reorder point Peradventure your distributor or wholesaler cannot fulfill your order or think there will be a delay, you can assign an automated reorder point. You can also provide the option of refunding payment if the customer cannot wait for the order. You need to know when you are running short of inventory. Assign reorder dates; this can be weekly, monthly, or increments. With this, the system can keep track of items in stock.